Check Out the Globe of Light Weight Aluminum Spreading: Expert Keys and Strategies
In the world of manufacturing, aluminum casting stands as an essential procedure, vital for the creation of a wide range of products. Behind the relatively simple strategy exist a wide range of detailed elements, frequently unbeknownst to several. As we browse through the world of light weight aluminum casting, there exists a realm of insider keys and methods that can elevate the top quality of the end products and enhance the production process. By revealing these concealed gems and checking out the subtleties of this craft, an entire new dimension of possibilities arises, promising to change the way we perceive and involve with aluminum spreading.
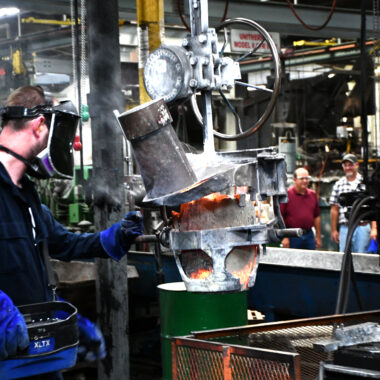
The Fundamentals of Light Weight Aluminum Spreading
Aluminum spreading, a basic process in manufacturing, involves the putting of molten light weight aluminum right into a mold and mildew to attain wanted shapes and structures. This versatile method is extensively used throughout numerous sectors as a result of aluminum's outstanding buildings such as high strength-to-weight ratio, corrosion resistance, and thermal conductivity.
The procedure begins with the melting of light weight aluminum in a heater at temperature levels exceeding 1220 ° F(660 ° C ) Once the light weight aluminum reaches its fluid state, it is poured right into a pre-designed mold and mildew cavity. The mold, typically made from products like steel or sand, determines the last shape of the cast aluminum component.
After putting, the light weight aluminum is left to strengthen and cool down within the mold - about aluminum casting. This cooling period is essential as it establishes the stability and quality of the last item. Once solidified, the mold and mildew is gotten rid of, disclosing the freshly formed light weight aluminum spreading
Insider Tips for Successful Casting
To achieve ideal outcomes in light weight aluminum spreading, meticulous attention to information throughout the mold layout stage is vital for ensuring effective end results. Surveillance and controlling the metal temperature level throughout the casting process can assist protect against problems such as early solidification or porosity in the final item.
Additionally, an additional key pointer is to effectively prepare the mold and mildew surface area. A well-prepared mold and mildew surface area can contribute to far better metal flow, decreased turbulence, and boosted surface area finish on the cast part. This preparation may include using finishes or therapies to enhance mold and mildew release and avoid metal/mold interactions that can result in flaws. By paying close focus to these expert pointers, manufacturers can improve the top quality and performance of their light weight aluminum casting processes.
Advanced Strategies in Aluminum Spreading
Using ingenious techniques and cutting-edge techniques, the realm of aluminum spreading has seen a significant development towards advanced techniques that press the boundaries of conventional techniques. One such technique is vacuum cleaner spreading, which entails producing a vacuum atmosphere to get rid of air from the mold dental caries, causing greater high quality and more elaborate castings with minimized porosity. In addition, investment casting, also known as lost-wax casting, is a refined method that enables intricate shapes and thin walls, leading to accurate and comprehensive light weight aluminum parts.
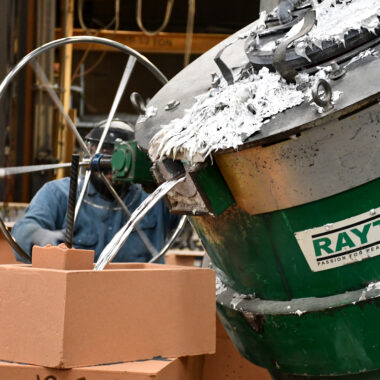
Moreover, advanced simulation software application plays an important role in enhancing spreading styles and forecasting possible defects, permitting adjustments to be made before the actual casting procedure starts. By embracing these advanced strategies, suppliers can boost their light weight aluminum casting capabilities to new elevations, satisfying the demands of contemporary sectors with precision and technology.
Understanding Various Casting Approaches
In the world of production, an extensive understanding of different casting methods is essential for accomplishing optimum outcomes in steel fabrication processes. Various spreading approaches supply unique benefits and are chosen based on factors such as the intricacy of the design, production quantity, product demands, and cost factors to consider. Among one of the most usual spreading methods is sand casting, where a mold and mildew is created using sand as the key product. Sand spreading is functional, affordable, and suitable for producing large parts.
An additional prominent casting method is pass away spreading, which involves infusing molten steel right into a mold dental caries under high stress. Pass away spreading is understood for its high precision, smooth surface area coating, and the ability to create intricate forms with tight resistances. Gravity spreading, on the other hand, depends on gravity to load the mold and mildew cavity with liquified metal. This approach appropriates for producing less complex forms and is cost-efficient for small to tool production runs. By understanding the subtleties of various spreading approaches, manufacturers can make educated decisions to enhance their manufacturing procedures and accomplish the wanted results.
Making Best Use Of Efficiency in Spreading Operations
With a strong grasp of the subtleties of various spreading techniques, producers can enhance their procedures to boost performance in metal fabrication processes. Optimizing effectiveness in casting procedures calls for a systematic strategy that concentrates on optimizing every action of the casting procedure.
In addition, spending in innovative innovation and equipment can dramatically boost performance in casting procedures. Automated systems, robotics, and computer-aided style (CAD) software program can improve procedures, minimize errors, and boost output. Furthermore, training employees on the latest strategies and ideal techniques try this web-site can also add to maximizing efficiency in casting procedures.
Routine maintenance of tools and devices is useful site crucial to decrease and prevent malfunctions downtime - about aluminum casting. Implementing a positive maintenance timetable can aid determine prospective issues prior to they rise, making sure smooth operations and undisturbed production. In general, by prioritizing performance and continual renovation, makers can enhance their spreading operations and remain competitive in the sector

Conclusion
In verdict, the globe of aluminum spreading uses a wide array of chances for those looking to produce long lasting and intricate metal things. Understanding the numerous spreading techniques and enhancing performance in procedures are key parts to accomplishing top quality outcomes in aluminum spreading.
One such method is vacuum cleaner casting, which entails creating a vacuum cleaner atmosphere to remove air from the mold cavity, leading to higher top quality and more intricate spreadings with decreased porosity (about aluminum casting). Furthermore, investment casting, also known as lost-wax spreading, is a polished approach that enables for complex shapes and thin wall surfaces, resulting in thorough and accurate light weight aluminum components
One of the most usual spreading approaches is sand casting, where a mold and mildew is created using sand as the key product.One more popular spreading approach is pass away casting, you could check here which includes injecting liquified metal right into a mold cavity under high stress. Comprehending the different casting methods and maximizing performance in procedures are crucial elements to attaining premium outcomes in light weight aluminum casting.